Concrete is a critical structural element, and its strength directly impacts a building’s safety. But how do we ensure it meets the demands placed upon it? Concrete strength testing ensures a concrete mix meets design specifications for its intended load-bearing capacity, to ensure the structure’s stability and prevent potential failures.
Concrete strength is most commonly measured by testing its compressive strength, which measures its ability to withstand forces pushing it inwards and together. This article reviews methods for testing concrete strength, both in the controlled environment of a lab and on-site in the field. We’ll also explore preparation methods used for the concrete test specimens and other concrete tests indirectly related to strength.
Q: What units are used when concrete compressive strength is measured?
A: Concrete compressive strength is measured in pounds per square inch (psi) in the U.S. or megapascals (MPa) in the metric system. A higher psi or MPa value indicates a stronger concrete.
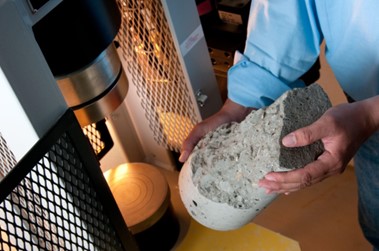
Lab Testing: Strength Testing & Related Tests During Planning and Pre-Construction
Lab testing a calculation of concrete strength under controlled conditions. It is typically used for initial mix design and strength evaluation during planning and pre-construction or to help with batching quality control.
Note: While lab samples can be useful, they might not exactly replicate the actual curing conditions on the construction site. Enter the need for field testing for verifying in-situ strength, which will be discussed later in this article.
Lab Concrete Strength Cylinder Test (ASTM C39): This lab test measures a concrete cylinder’s ability to withstand a compressive load until failure and is the primary method used by engineers for determining concrete strength. Cylinders are cast from the fresh concrete mix and cured under controlled temperature and humidity conditions which mimic the actual construction site environment. After a specified period (usually 7 or 28 days), the cylinders are crushed in a hydraulic press. This machine applies a compressive force on the ends of the cylinder, gradually increasing the pressure, until the cylinder cracks or breaks.
The maximum load it can bear is then recorded. The load is divided by the cylinder’s cross-sectional area to obtain the compressive strength. This compressive strength value becomes a benchmark for the concrete’s overall strength.
The desired compressive strength will depend on the intended use for the concrete. Sidewalk and driveway projects, for example, may require a lower psi than commercial buildings and warehouses.
Field cylinders may also undergo the ASTM C39 test (see: Making and Curing Test Specimens (ASTM C31) below for more detail). Field cylinders evaluate the concrete’s actual strength “in-situ” within the structure, while lab cylinders assess the mix design’s potential under controlled conditions.
Unbonded Capping of Concrete Cylinders (ASTM C1231):
In concrete strength testing, unbonded capping is an alternative method for preparing the ends of cylindrical concrete specimens so that they are flat. For an accurate test, the top and bottom faces of the cylinder must be perpendicular to its axis. Uneven load-bearing surfaces can introduce errors in the test results.
Unbonded capping uses a flexible pad, typically neoprene or rubber, instead of a bonded capping material like sulfur mortar or neat cement paste. The pad is placed on each end of the concrete cylinder and steel retainer rings hold the pads securely in place to create a smooth, flat surface.
Unbonded caps are quicker to apply and remove (vs. grinding or cutting uneven ends or bonded capping) for faster preparation of specimens before each test The pads may be reused up to 100 times, reducing waste and cost (vs. single-use bonded caps).
However, unbonded capping cannot be used in every case. ASTM C1231 outlines limitations for using unbonded caps. They are generally not suitable for very low (below 10 MPa or 1500 psi) or very high strength (above 80 MPa or 12000 psi) concrete. Unbonded caps are suitable for concrete with minor imperfections on the ends, up to 5 mm (around 3/16 inches). For larger deviations, grinding or cutting the cylinder ends might be necessary before testing.
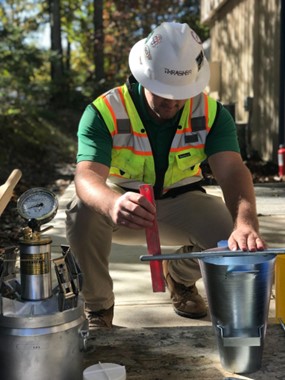
Field Testing: Assessing In-Situ Strength
While lab testing provides valuable insights for planning and pre-construction, construction also requires assessing the strength of concrete after it has been poured and cured on-site in actual field conditions. Field testing is key for investigating potential concrete strength issues in existing structures – especially when quick confirmation of adequate strength is needed for construction progress.
Below are a few key strength-related concrete field testing methods and processes:
Slump Test (ASTM C143): The Slump Test is a quick test that measures the consistency and workability of fresh (unhardened) cement concrete, which impacts its compaction and ultimately, its strength. Concrete with a higher slump may be easier to place but can lead to trapped air and reduced strength. The Slump Test is a valuable tool for concrete quality control in the field, ensuring the correct consistency (not too wet or too dry) and cohesion (the ingredients are holding together well).
To conduct the Slump Test, a cone-shaped mold is filled with concrete in layers and rodded to remove air bubbles. The mold is lifted straight up, and the slump is the distance that the center of the concrete settles. This indicates how easily the concrete will flow and fill forms, with a moderate slump (between 1/2 inch and 9 inches) being ideal for most applications.
Sampling of Freshly Mixed Concrete (ASTM C172): Obtaining a representative sample of fresh concrete ensures accurate concrete strength testing. Following ASTM C172 ensures a well-mixed composite sample that accurately reflects the overall properties of the concrete batch for reliable strength testing. Samples are taken from the middle portion of the concrete batch, avoiding the first and last portions that may not be well mixed.
For portable drum mixers and mixer trucks, sampling occurs during discharge, when a container is inserted into the stream, or the concrete flow is diverted into a container during discharge. For paving mixers, samples are collected from five locations after the entire contents of the paving mixer are discharged onto the ground where the concrete will be placed.
Regardless of the mixer type, it’s crucial to collect the sample within the specified timeframe (usually 15 minutes after obtaining the first portion) to ensure the properties haven’t changed significantly.
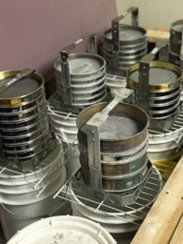
Making and Curing Test Specimens (ASTM C31): ASTM C31 outlines the process for making and curing cylindrical or beam-shaped concrete test specimens in the field. Fresh concrete is obtained following ASTM C172 and placed in molds in layers. Each layer is rodded to eliminate air bubbles, and the top is smoothed. The molds are covered to prevent moisture loss and kept at a specific temperature range for an initial curing period. Then, the specimens are demolded and submerged in water or a limewater solution for final curing until testing, typically at 28 days. This ensures the concrete reaches a controlled and standardized strength for accurate compressive strength test results.
Temperature of Concrete (ASTM C1064): ASTM C1064 is a standard test method for determining the temperature of freshly mixed concrete at the time of placement. It outlines how to measure the temperature using a specific type of thermometer that can be inserted into the concrete. The field concrete test ensures the concrete is within a proper temperature range (typically between 30°F and 120°F or 0°C and 50°C). This is important for concrete strength because extreme temperatures can affect the setting time, workability, and thus, the ultimate strength of the concrete.
Unit Weight (ASTM C138): ASTM C138 is a test method to determine the unit weight (also sometimes referred to as density) of fresh concrete. Unit weight is important for estimating yield of concrete from a mix design (knowing the unit weight allows engineers to calculate the actual volume of the resulting concrete from the ingredients) and quality control (unit weight variations can indicate potential issues with the mix proportions, mixing process or presence of air bubbles).
The test involves filling a specific mold with the fresh concrete and compacting it according to the standard. The weight of the filled mold is then measured, and dividing this weight by the known volume of the mold gives the unit weight of the concrete.
This test has an indirect relationship to concrete strength. Higher unit weight typically indicates a denser concrete mix with fewer air pockets, which usually means a higher strength. However, it’s not a standalone measure of strength. For example, a concrete mix with a higher unit weight due to the amount of heavy aggregate might not necessarily be stronger than a mix with a lower unit weight that has a more optional mix design.
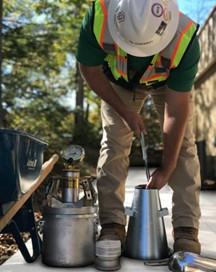
Air Content by Pressure Method (ASTM C231): The Air Content by Pressure Method test measures the volume of air entrapped within the concrete mix and is used for concrete made with relatively dense aggregate particles, excluding internal air voids within the aggregates themselves. The pressure method test uses a special apparatus called an air meter, which is filled with a concrete sample and water. The air meter bucket rim is cleaned and the top section is placed, after which sealed water is introduced through one of either petcocks until all air bubbles dissipate, then the petcocks are closed. Air pressure is applied, and the change in volume of the trapped air is measured. Maintaining the desired air content is crucial for ensuring concrete durability, workability, and achieving the target strength. Too little air can lead to freeze-thaw damage, while too much air can reduce strength.
Air Content by Volumetric Method (ASTM C173): The Air Content by Volumetric Method outlined in ASTM C173 is a test to measure the air trapped within fresh concrete. This test helps ensure the concrete has the proper amount of air for workability and freeze-thaw resistance. Its value lies in its ability to accurately measure air content in concrete where the air content by pressure method might struggle, such as lightweight concrete and those with highly porous aggregates. Generally, higher air content leads to lower strength, however it is not a direct measure of concrete strength.
For this test, concrete is placed in the meter bucket in two layers, rodded and sides tapped for each layer. The bucket rim is cleaned, and the graduated neck is placed on the bucket and clamped for a tight seal. The funnel is then placed in the neck and a small amount of water is added before introducing 2 pt of 70% isopropyl alcohol, then the remaining water is added up to the 0 mark. Then the top is added and sealed into place.
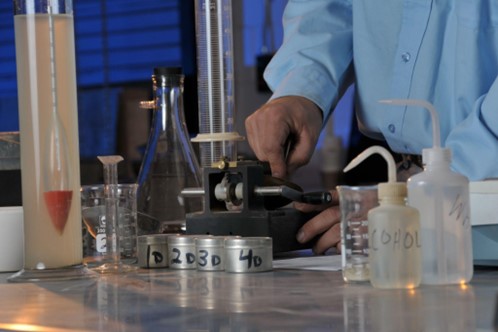
The meter is then shaken and rolled to release air bubbles. The water level in the neck rises due to the displaced air, and this change in level indicates the air content as a percentage of the total concrete volume. This test helps ensure the concrete has the proper amount of air for workability and freeze-thaw resistance.
Ready to begin testing?
By employing a combination of these tests, engineers gain a comprehensive understanding of concrete’s properties, ensuring a safe and structurally sound construction project. Need concrete strength testing services or other concrete construction materials testing? Contact The Thrasher Group NC about our AASHTO and CCRL accredited test lab and services.